تولید نفت در میادین نفتی
خطوط کنترل در چاه چگونه کار می کند؟
خطوط کنترل انتقال سیگنالها را امکانپذیر میسازند، امکان جمعآوری دادههای پایین چاه را فراهم میکنند و اجازه کنترل و فعالسازی ابزارهای پایین چاه را میدهند.
سیگنالهای فرمان و کنترل را میتوان از یک مکان روی سطح به ابزار پایین چاه در چاه فرستاد.داده های حسگرهای چاه را می توان برای ارزیابی یا استفاده در عملیات چاه های خاص به سیستم های سطحی فرستاد.
شیرهای ایمنی Downhole (DHSVs) شیرهای ایمنی زیرسطحی با کنترل سطح (SCSSV) هستند که به صورت هیدرولیکی از یک صفحه کنترل روی سطح کار می کنند.هنگامی که فشار هیدرولیک به پایین یک خط کنترل اعمال می شود، فشار یک آستین در شیر را مجبور می کند تا به پایین بلغزد و دریچه را باز می کند.با آزاد شدن فشار هیدرولیک، شیر بسته می شود.
خطوط هیدرولیک داون هول Meilong Tube عمدتاً به عنوان مجرای ارتباطی برای دستگاه های پایین چاه هیدرولیکی در چاه های تزریق نفت، گاز و آب مورد استفاده قرار می گیرد، جایی که دوام و مقاومت در برابر شرایط شدید مورد نیاز است.این خطوط را می توان برای انواع برنامه ها و اجزای پایین چاه پیکربندی کرد.
تمام مواد محصور شده از نظر هیدرولیتیکی پایدار هستند و با تمام سیالات تکمیل چاه معمولی از جمله گاز فشار بالا سازگار هستند.انتخاب مواد بر اساس معیارهای مختلفی از جمله دمای کف چاله، سختی، استحکام کششی و پارگی، جذب آب و نفوذپذیری گاز، اکسیداسیون و مقاومت در برابر سایش و شیمیایی انجام می شود.
خطوط کنترل توسعه گسترده ای را تجربه کرده اند، از جمله آزمایش خرد کردن و شبیه سازی چاه اتوکلاو فشار بالا.آزمایشهای خرد شدن آزمایشگاهی بارگذاری افزایش یافته را نشان دادهاند که تحت آن لولههای محصور شده میتوانند یکپارچگی عملکردی خود را حفظ کنند، به ویژه در مواردی که از سیمهای سپر رشته سیم استفاده میشود.
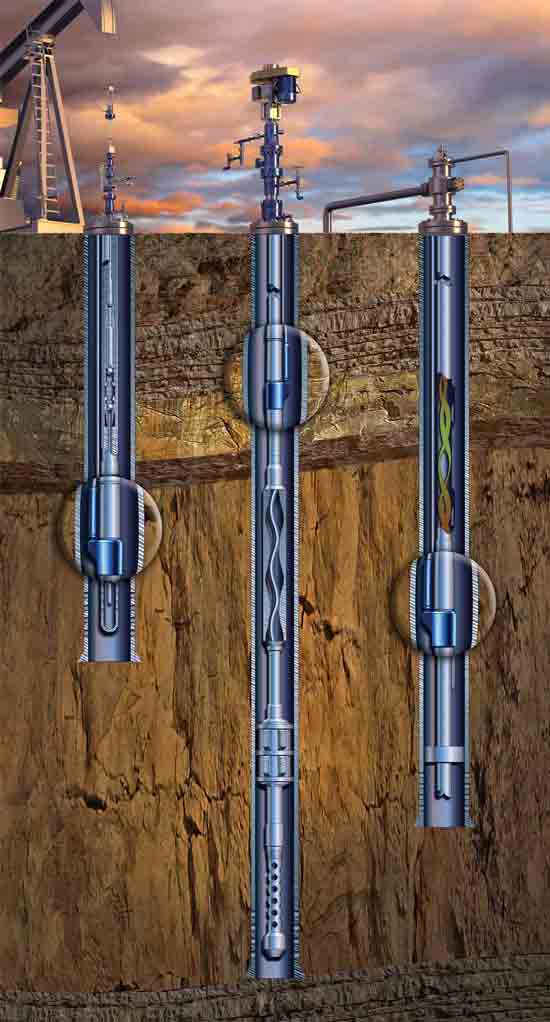
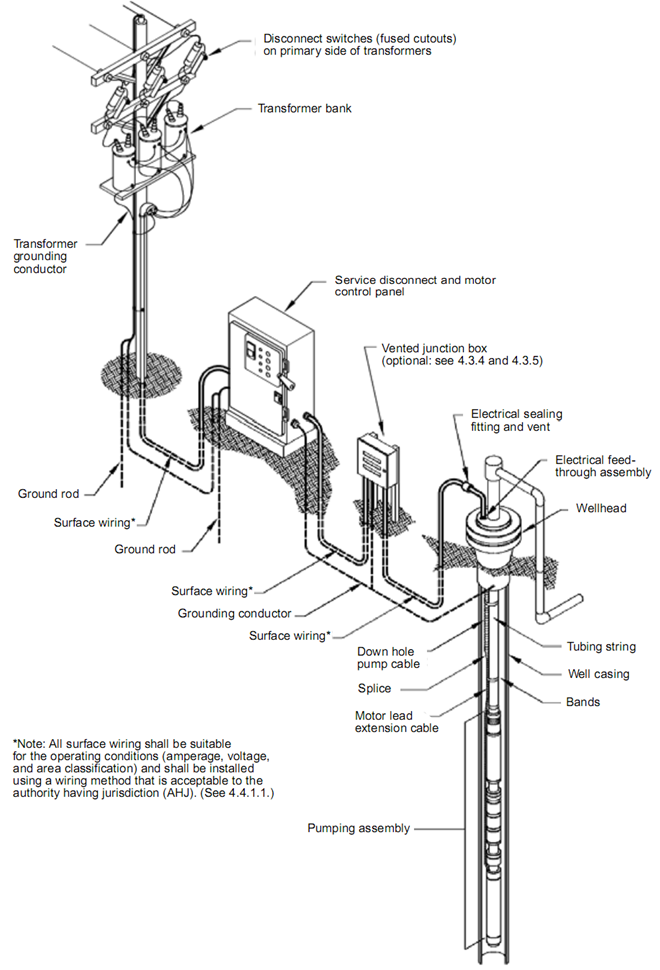
خطوط کنترل در کجا استفاده می شود؟
چاههای هوشمندی که به دلیل هزینهها یا خطرات مداخلات یا ناتوانی در پشتیبانی از زیرساختهای سطحی مورد نیاز در یک مکان دور، به عملکرد و مزایای مدیریت مخزن دستگاههای کنترل جریان از راه دور نیاز دارند.
★ زمین، سکو، یا محیط های زیر دریا.
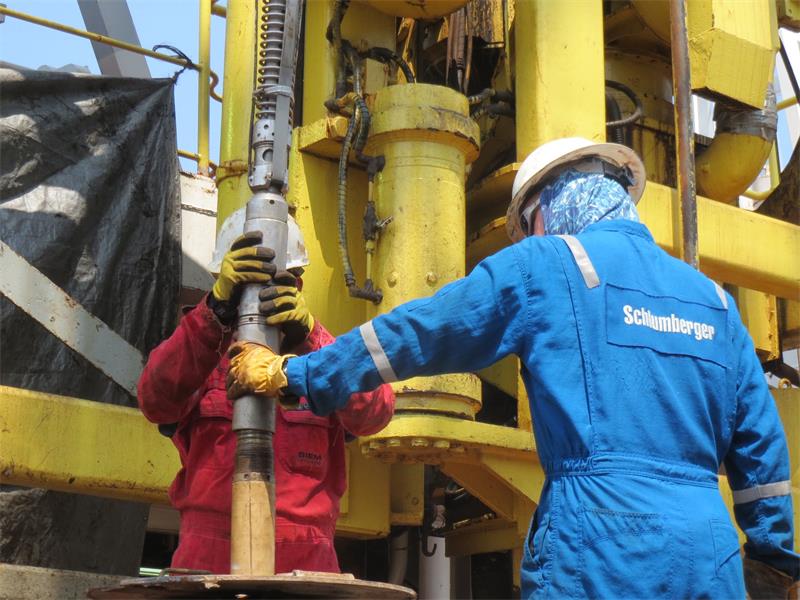
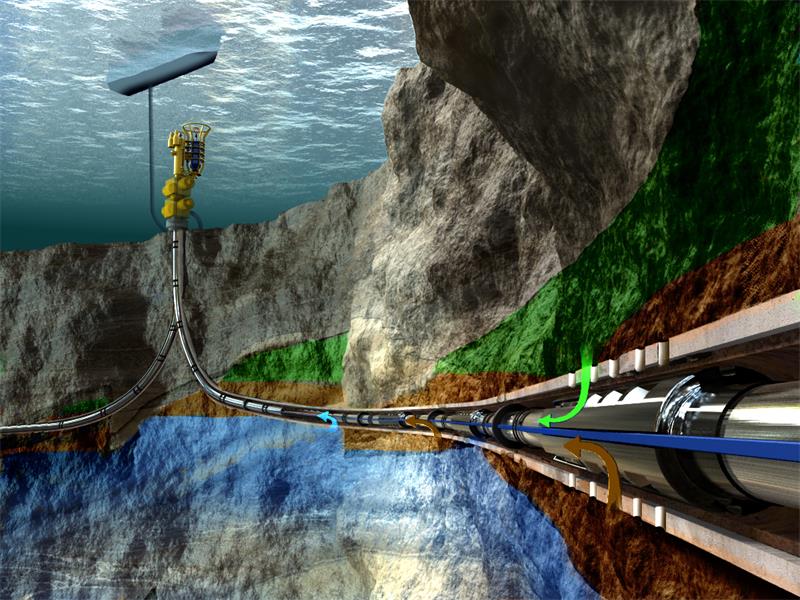
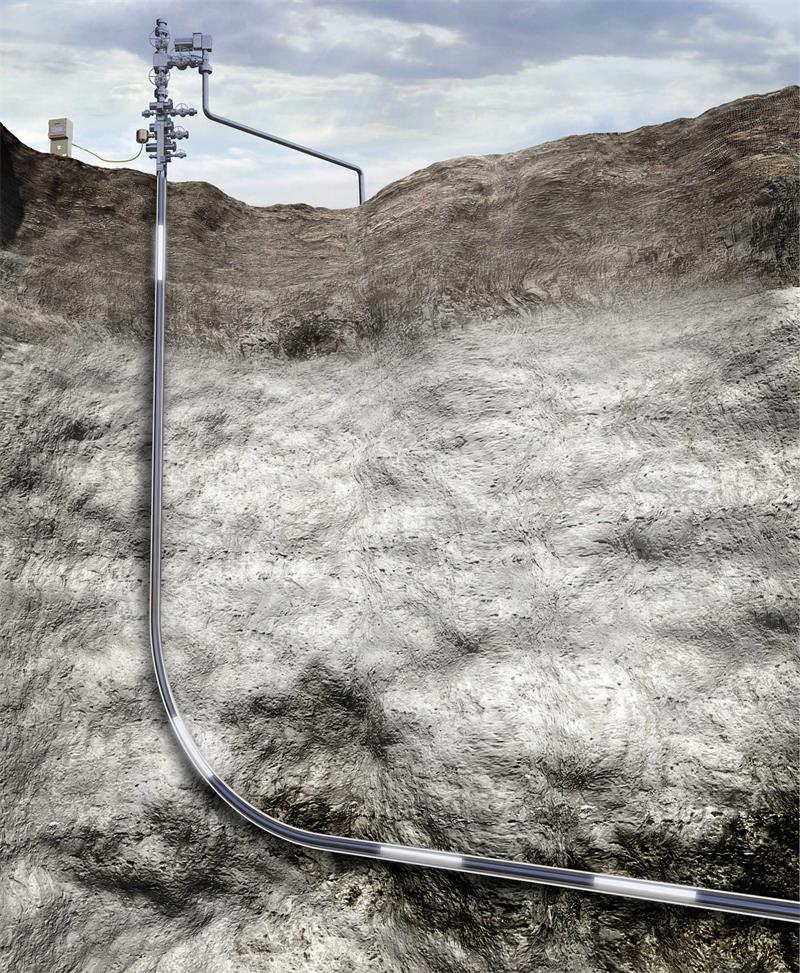
تولید برق زمین گرمایی
انواع گیاهان
اساساً سه نوع نیروگاه زمین گرمایی برای تولید برق استفاده می شود.نوع گیاه در درجه اول با توجه به ماهیت منبع زمین گرمایی در سایت تعیین می شود.
به اصطلاح نیروگاه زمین گرمایی بخار مستقیم زمانی استفاده می شود که منبع زمین گرمایی بخار را مستقیماً از چاه تولید کند.بخار پس از عبور از جداکننده ها (که ذرات ریز ماسه و سنگ را حذف می کنند) به توربین هدایت می شود.اینها اولین انواع گیاهان بودند که در ایتالیا و در ایالات متحده توسعه یافتند.بدیهی است که نیروگاه های بخار برای منابع با دمای پایین استفاده نمی شوند.
نیروگاه های بخار فلاش در مواردی استفاده می شوند که منبع زمین گرمایی آب گرم با دمای بالا یا ترکیبی از بخار و آب گرم تولید می کند.سیال از چاه به یک فلاش تانک تحویل داده می شود که در آنجا بخشی از آب به بخار تبدیل می شود و به سمت توربین هدایت می شود.آب باقیمانده به سمت دفع هدایت می شود (معمولاً تزریق).بسته به دمای منبع ممکن است بتوان از دو مرحله فلاش تانک استفاده کرد.در این حالت، آب جدا شده در مخزن مرحله اول به یک فلاش تانک مرحله دوم هدایت می شود که در آن بخار بیشتر (اما با فشار کمتر) جدا می شود.سپس آب باقیمانده از مخزن مرحله دوم به سمت دفع هدایت می شود.به اصطلاح کارخانه دوبل فلاش بخار را با دو فشار متفاوت به توربین می رساند.باز هم این نوع گیاه را نمی توان برای منابع با دمای پایین اعمال کرد.
سومین نوع نیروگاه زمین گرمایی، نیروگاه دوتایی نام دارد.این نام از این واقعیت گرفته شده است که یک سیال دوم در یک چرخه بسته به جای بخار زمین گرمایی برای کار کردن توربین استفاده می شود.شکل 1 یک نمودار ساده از یک نیروگاه زمین گرمایی نوع دوتایی را نشان می دهد.سیال زمین گرمایی از یک مبدل حرارتی به نام دیگ بخار یا بخارساز عبور داده می شود (در برخی کارخانه ها، دو مبدل حرارتی به صورت سری اولی پیش گرمکن و دومی بخارساز) که در آن گرمای موجود در سیال زمین گرمایی به سیال کار منتقل می شود و باعث جوشیدن آن می شود. .سیالات کاری گذشته در گیاهان دوتایی دمای پایین، مبردهای CFC (نوع فریون) بودند.ماشینهای فعلی از هیدروکربنها (ایزوبوتان، پنتان و غیره) مبردهای نوع HFC با سیال خاصی که برای مطابقت با دمای منابع زمین گرمایی انتخاب شدهاند، استفاده میکنند.
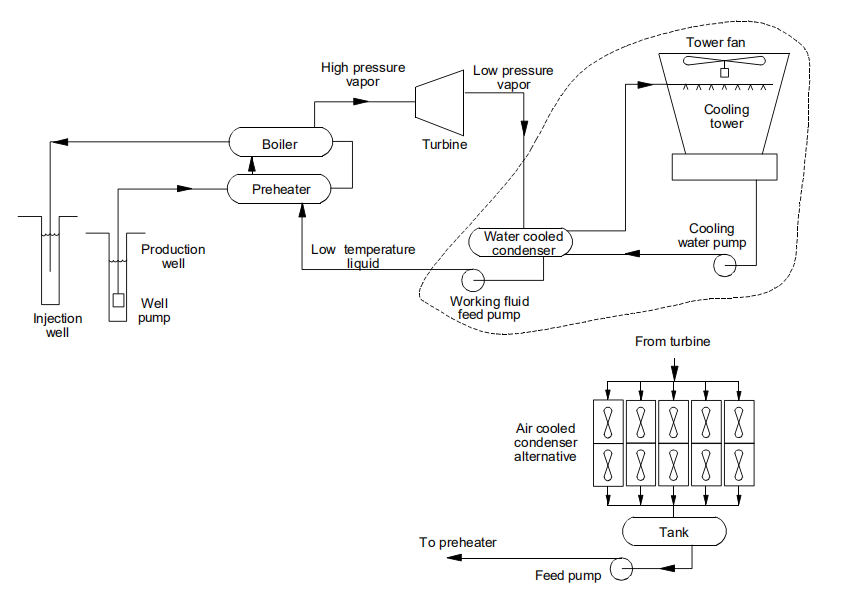
شکل 1. نیروگاه دوتایی زمین گرمایی
بخار سیال عامل به توربین منتقل می شود که در آنجا محتوای انرژی آن به انرژی مکانیکی تبدیل می شود و از طریق شفت به ژنراتور تحویل می شود.بخار از توربین به کندانسور خارج می شود و در آنجا دوباره به مایع تبدیل می شود.در اکثر گیاهان، آب خنک کننده بین کندانسور و برج خنک کننده به گردش در می آید تا این گرما را به جو دفع کند.یک جایگزین استفاده از کولرهای خشک یا کندانسورهای هوا خنک است که گرما را مستقیماً بدون نیاز به آب خنک کننده به هوا دفع می کنند.این طرح اساساً هرگونه استفاده مصرفی گیاه از آب برای خنک کردن را حذف می کند.خنک کاری خشک، زیرا در دماهای بالاتر (مخصوصاً در فصل کلیدی تابستان) نسبت به برجهای خنککننده کار میکند، بازده کارخانه را کاهش میدهد.سیال کار مایع از کندانسور توسط پمپ تغذیه به پیش گرمکن/بخارساز فشار بالاتر پمپ می شود تا چرخه تکرار شود.
چرخه دودویی نوع گیاهی است که برای کاربردهای زمین گرمایی با دمای پایین استفاده می شود.در حال حاضر، تجهیزات باینری خارج از قفسه در ماژول های 200 تا 1000 کیلووات موجود است.
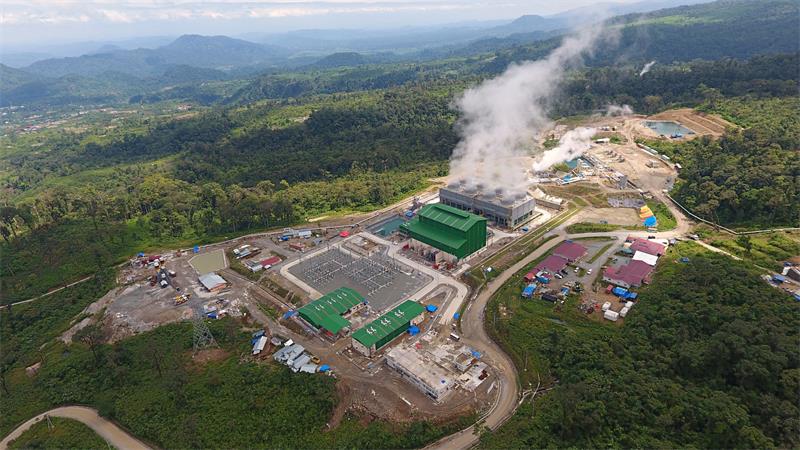
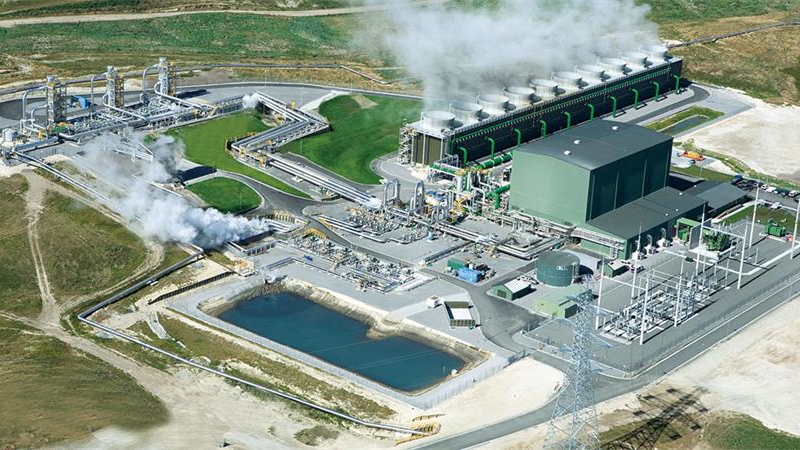
اصول نیروگاه
اجزای نیروگاه
فرآیند تولید الکتریسیته از یک منبع گرمایی زمین گرمایی با دمای پایین (یا از بخار در یک نیروگاه معمولی) شامل فرآیندی است که مهندسان از آن به عنوان چرخه رانکین یاد می کنند.در یک نیروگاه معمولی، چرخه، همانطور که در شکل 1 نشان داده شده است، شامل یک دیگ بخار، توربین، ژنراتور، کندانسور، پمپ آب تغذیه، برج خنک کننده و پمپ آب خنک کننده است.بخار در دیگ با سوزاندن سوخت (زغال سنگ، نفت، گاز یا اورانیوم) تولید می شود.بخار به توربین منتقل می شود که در آن هنگام انبساط در برابر پره های توربین، انرژی گرمایی بخار به انرژی مکانیکی تبدیل می شود و باعث چرخش توربین می شود.این حرکت مکانیکی از طریق یک شفت به ژنراتور منتقل می شود و در آنجا به انرژی الکتریکی تبدیل می شود.بخار پس از عبور از توربین دوباره به آب مایع در کندانسور نیروگاه تبدیل می شود.از طریق فرآیند تراکم، گرمای استفاده نشده توسط توربین به آب خنک کننده رها می شود.آب خنککننده به برج خنککننده منتقل میشود، جایی که «گرمای اتلاف» از چرخه به اتمسفر دفع میشود.میعانات بخار توسط پمپ تغذیه برای تکرار فرآیند به دیگ بخار تحویل داده می شود.
به طور خلاصه، نیروگاه به سادگی چرخه ای است که تبدیل انرژی از یک شکل به شکل دیگر را تسهیل می کند.در این حالت انرژی شیمیایی موجود در سوخت به گرما (در دیگ بخار) و سپس به انرژی مکانیکی (در توربین) و در نهایت به انرژی الکتریکی (در ژنراتور) تبدیل می شود.اگرچه محتوای انرژی محصول نهایی، الکتریسیته، معمولاً بر حسب واحد وات ساعت یا کیلووات ساعت (1000 وات ساعت یا 1 کیلووات ساعت) بیان میشود، اما محاسبات عملکرد نیروگاه اغلب بر حسب واحد BTU انجام میشود.به یاد داشته باشید که 1 کیلووات ساعت معادل انرژی 3413 BTU است.یکی از مهمترین معیارها در مورد نیروگاه این است که چه مقدار انرژی ورودی (سوخت) برای تولید یک خروجی الکتریکی مورد نیاز است.
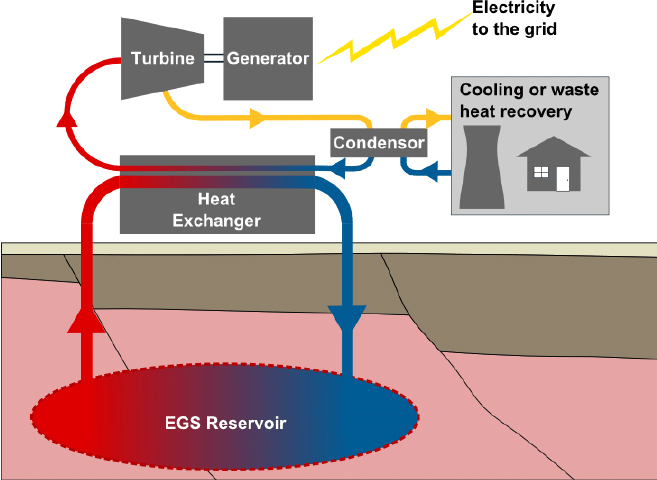
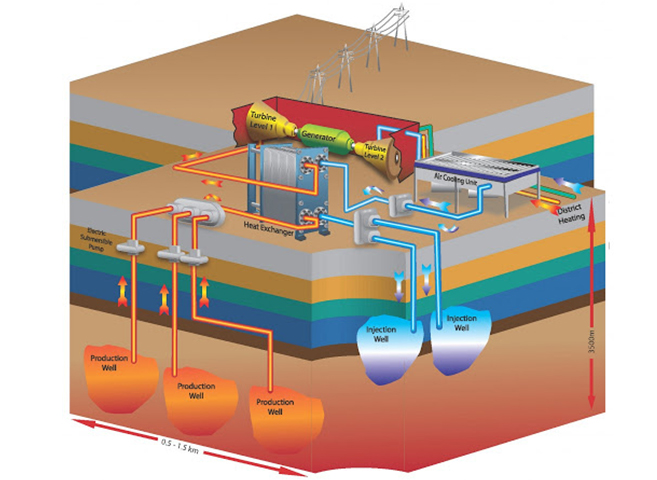
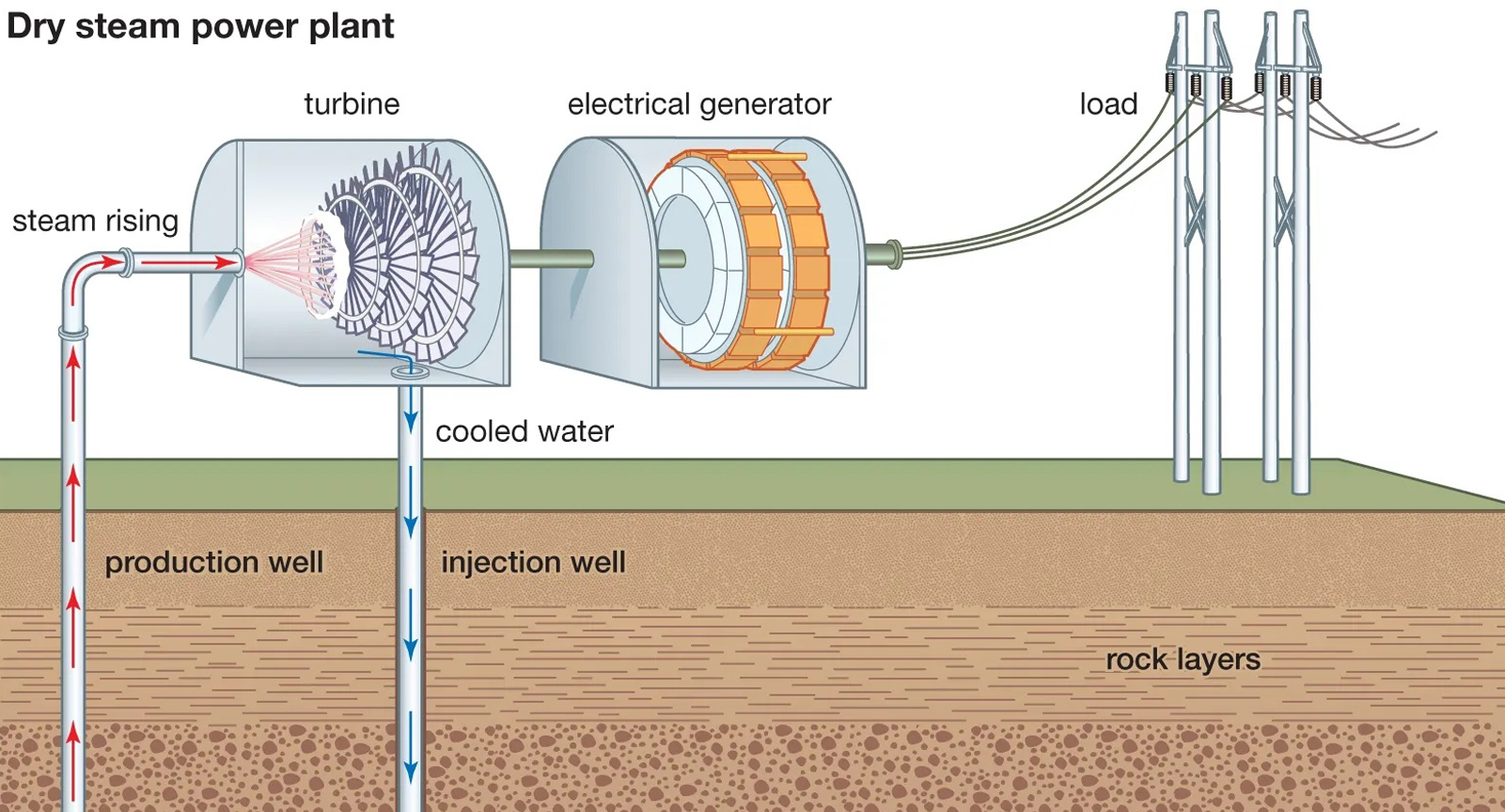
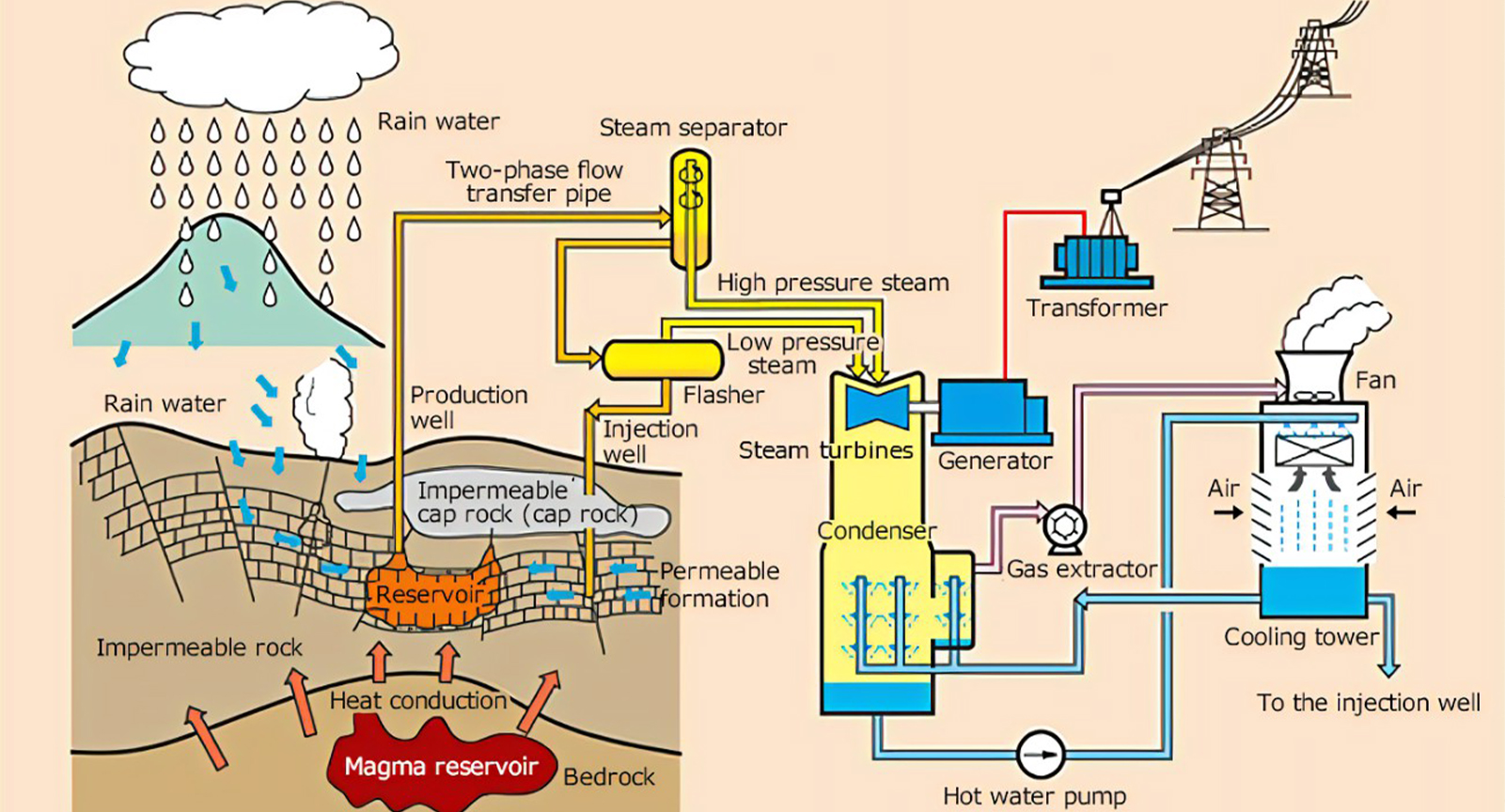
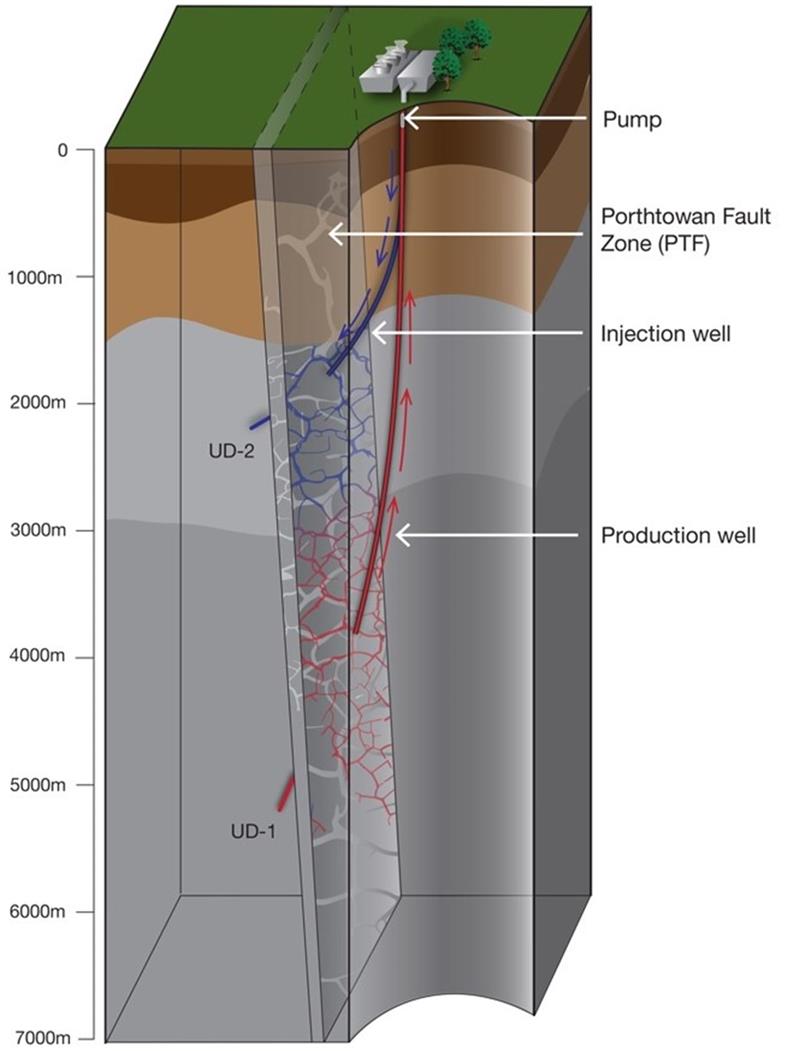
ناف زیر دریا
توابع اصلی
تامین نیروی هیدرولیک برای سیستم های کنترل زیر دریا، مانند باز کردن/بستن دریچه ها
ارائه قدرت الکتریکی و سیگنال های کنترل به سیستم های کنترل زیر دریا
مواد شیمیایی تولیدی را برای تزریق در زیر دریا در درخت یا چاله تحویل دهید
گاز را برای عملیات بالابر گاز تحویل دهید
برای ارائه این عملکرد، یک ناف آب عمیق می تواند شامل شود
لوله های تزریق مواد شیمیایی
لوله های تامین هیدرولیک
کابل های سیگنال کنترل الکتریکی
کابل های برق
سیگنال فیبر نوری
لوله های بزرگ برای بالابر گاز
ناف زیر دریا مجموعهای از شیلنگهای هیدرولیک است که میتواند شامل کابلهای الکتریکی یا فیبرهای نوری نیز باشد که برای کنترل سازههای زیر دریا از یک سکوی دریایی یا یک کشتی شناور استفاده میشود.این یک بخش اساسی از سیستم تولید زیردریایی است که بدون آن تولید پایدار نفت زیر دریا ممکن نیست.
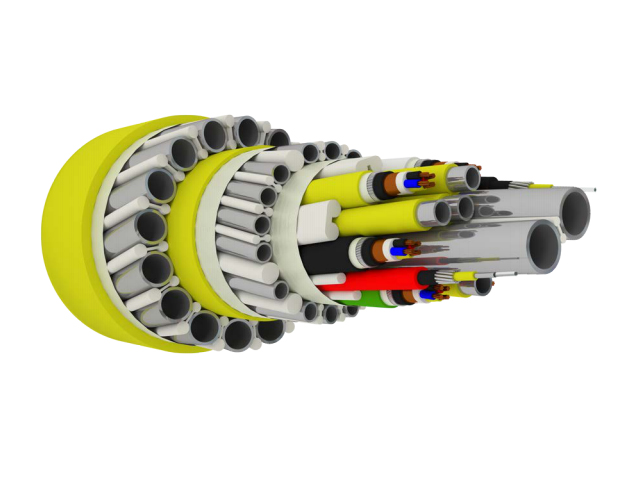
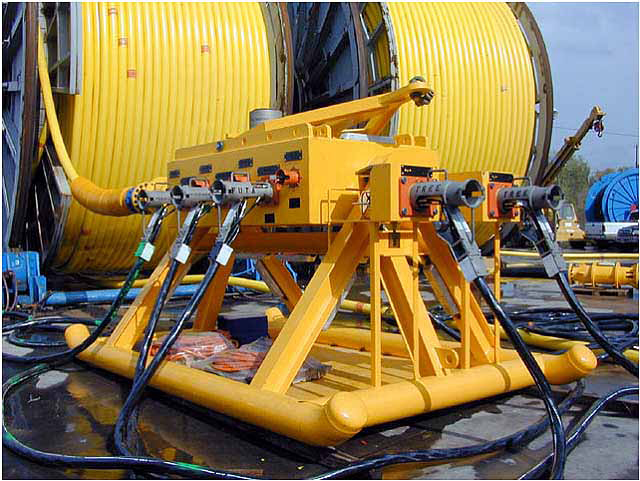
اجزای کلیدی
بند ناف تاپساید (TUTA)
مجموعه پایان ناف تاپسید (TUTA) رابط بین تجهیزات کنترل ناف اصلی و قسمت بالایی را فراهم می کند.این واحد یک محفظه ایستاده آزاد است که میتواند در مکانی مجاور بند ناف در یک محیط در معرض خطر در قسمت بالای دستگاه پیچ یا جوش داده شود.این واحدها معمولاً با توجه به نیازهای مشتری با دید هیدرولیک، پنوماتیک، قدرت، سیگنال، فیبر نوری و انتخاب مواد ساخته می شوند.
TUTA معمولاً جعبه های اتصال الکتریکی را برای کابل های برق و ارتباط، و همچنین لوله کار، سنج ها و شیرهای بلوک و تخلیه برای منابع هیدرولیک و شیمیایی مناسب دارد.
مجمع ختم ناف (زیر دریا) (UTA)
UTA که در بالای یک پد گلی قرار دارد، یک سیستم الکتروهیدرولیک چند پیچه است که به بسیاری از ماژول های کنترل زیر دریا اجازه می دهد تا به همان خطوط ارتباطی، برق و هیدرولیک متصل شوند.نتیجه این است که بسیاری از چاه ها را می توان از طریق یک ناف کنترل کرد.از UTA، اتصالات به چاه ها و SCM های جداگانه با مجموعه های جامپر انجام می شود.
سرنخ های پرنده فولادی (SFL)
سرنخ های پرنده اتصالات الکتریکی/هیدرولیک/شیمیایی را از UTA به درختان/غلاف های کنترلی جداگانه فراهم می کنند.آنها بخشی از سیستم توزیع زیر دریا هستند که عملکردهای ناف را به اهداف خدماتی مورد نظرشان توزیع می کند.آنها معمولاً بعد از ناف نصب می شوند و توسط ROV متصل می شوند.
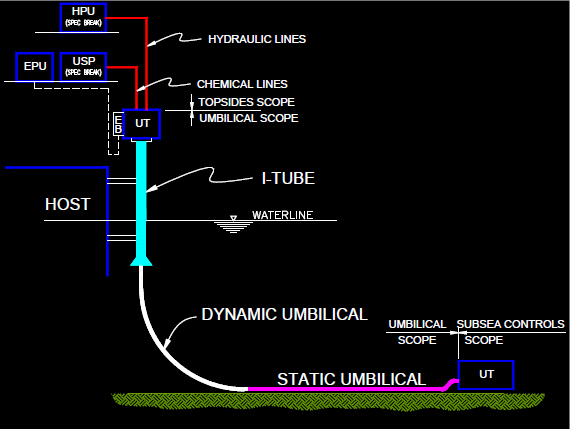
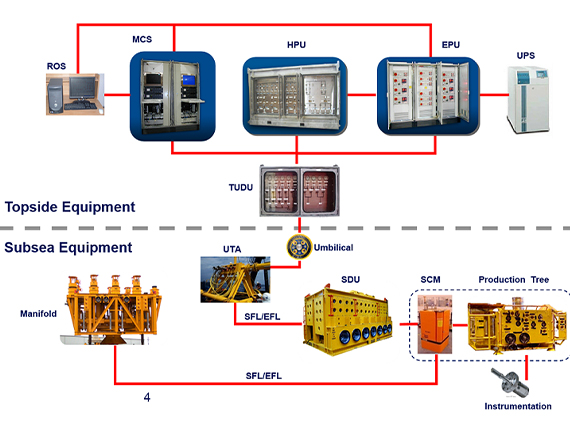
مواد ناف
بسته به نوع کاربرد، مواد زیر معمولاً در دسترس هستند:
ترموپلاستیک
مزایا: ارزان، تحویل سریع و مقاوم در برابر خستگی است
معایب: برای آب های عمیق مناسب نیست.مشکل سازگاری شیمیایی؛پیری و غیره
فولاد ضد زنگ Nitronic 19D دوبلکس با روکش روی
طرفداران:
هزینه کمتر در مقایسه با فولاد ضد زنگ فوق دوبلکس (SDSS)
قدرت تسلیم بالاتر در مقایسه با 316 لیتر
مقاومت در برابر خوردگی داخلی
سازگار برای خدمات تزریق هیدرولیک و مواد شیمیایی
واجد شرایط خدمات پویا
معایب:
حفاظت در برابر خوردگی خارجی مورد نیاز - روی اکسترود شده
نگرانی در مورد قابلیت اطمینان درزهای جوش در برخی از اندازه ها
لولهها سنگینتر و بزرگتر از SDSSهای مشابه هستند - نگرانیهای مربوط به نصب و راهاندازی آن
فولاد ضد زنگ 316 لیتر
طرفداران:
کم هزینه
برای مدت کوتاهی به حفاظت کاتدی کمی یا بدون نیاز است
قدرت تسلیم پایین
قابل رقابت با ترموپلاستیک برای فشار کم و آب کم عمق - ارزان تر برای عمر کوتاه در میدان
معایب:
برای سرویس پویا واجد شرایط نیست
حفره کلرید حساس است
فولاد ضد زنگ سوپر دوبلکس (معادل مقاومت حفره ای - PRE > 40)
طرفداران:
استحکام بالا یعنی قطر کم، وزن سبک برای نصب و آویزان کردن.
مقاومت بالا در برابر ترک خوردگی تنشی در محیط های کلرید (معادل مقاومت حفره ای > 40) به معنی عدم نیاز به پوشش یا CP است.
فرآیند اکستروژن به معنای عدم بازرسی جوش های درز دشوار است.
معایب:
تشکیل فاز بین فلزی (سیگما) در حین ساخت و جوشکاری باید کنترل شود.
بالاترین هزینه، طولانی ترین زمان تولید فولادهای مورد استفاده برای لوله های نافی
فولاد کربنی با روکش روی (ZCCS)
طرفداران:
هزینه کم نسبت به SDSS
واجد شرایط خدمات پویا
معایب:
درز جوش داده شده است
مقاومت در برابر خوردگی داخلی کمتر از 19D
قطر سنگین و بزرگ در مقایسه با SDSS
راه اندازی ناف
ناف هایی که به تازگی نصب شده اند معمولاً مایعات ذخیره ای در خود دارند.سیالات ذخیره سازی باید قبل از استفاده از محصولات مورد نظر، توسط محصولات مورد نظر خارج شوند.باید مراقب مشکلات احتمالی ناسازگاری بود که میتواند منجر به رسوب و بسته شدن لولههای ناف شود.اگر انتظار می رود ناسازگاری وجود داشته باشد، یک سیال بافر مناسب مورد نیاز است.به عنوان مثال، برای راه اندازی یک خط بازدارنده آسفالتین، یک حلال متقابل مانند EGMBE برای ایجاد بافر بین بازدارنده آسفالتین و مایع ذخیره سازی مورد نیاز است، زیرا آنها معمولاً ناسازگار هستند.